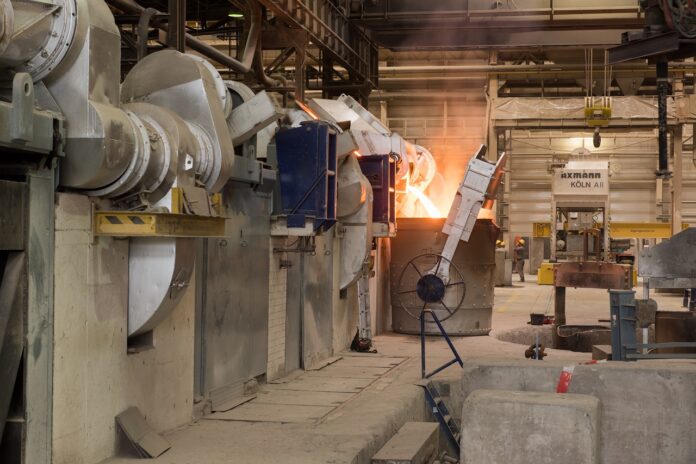
Die weltweite Schifffahrtbranche ist in den letzten zwei Jahrzehnten durch viele Krisen gegangen. Das spürte auch stets der europaweit letzte Zulieferer von größeren Schiffspropellern, die Mecklenburger Metallguss GmbH. Dennoch gelang es, auf Erfolgskurs zu bleiben – auch dank der Herauslösung aus einem Konzernverbund.
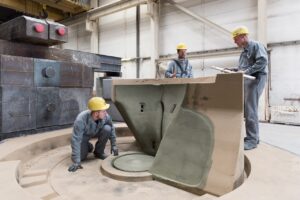
Von seinem Büro im vierten Stock des Verwaltungsgebäudes hat Dr.-Ing. Lars Greitsch, Geschäftsführer der Mecklenburger Metallguss GmbH, einen weiten Blick auf einen Großteil der Dreiseenstadt Waren an der Müritz. Unten im Hof lagern ausgediente Schiffspropellerflügel. „Diese schmelzen wir ein und gießen daraus neue Schiffspropeller. Dadurch haben wir immer genügend Material und müssen nicht auf den Rohstoffmärkten einkaufen“, sagt Greitsch. Schiffsschrauben bestehen aus einer speziellen Bronzelegierung mit dem Hauptelement Kupfer und besitzen vier bis sechs Flügel.
Hier in Waren werden vor allem große Schiffspropeller mit einem Gewicht von bis zu 120 Tonnen und einer durchschnittlichen Größe von bis zu zehn Metern im Sandgussverfahren gegossen. Die Warener sind Weltmarktführer bei der Fertigung von Schiffspropellern über 80 Tonnen Gewicht, 100 Stück werden dieses Jahr hergestellt. Eines der weltweit größten Kreuzfahrtschiffe, „Queen Mary 2“, wird mit Schiffsschrauben aus Waren angetrieben. Manchmal kann eine Schiffsschraube auch kleiner sein, muss aber besonders leise sein, wenn sie für ein U-Boot gebaut wird. Allen individuell gefertigten Schiffspropellern ist eines zu eigen: Sie müssen sich in rauer und schwerer See beweisen.
Hohe Fertigungstiefe gut für die Eigenkapitalquote
Das traf und trifft auch auf die Warener Produzenten zu. Mittlerweile sind sie der einzige Hersteller von Schiffspropellern in dieser Größenordnung in Europa; ein Produzent sitzt in Japan, zwei in Südkorea und sieben in China. Abzusehen war das nicht. Nach der Wende kam das Unternehmen im Rahmen der Privatisierung durch die Treuhandanstalt zum Konzernverbund der Bremer Vulkan-Werft, die allerdings durch ihre Zukäufe in Ostdeutschland schnell in die Schlagzeilen geriet. Ausgestattet mit üppigen Steuergeldern als Kaufanreiz dienten die Subventionen zur Kaschierung der Verluste an den westdeutschen Standorten mit der Begründung, die Gelder wären ins zentrale Cashmanagement der Bremer Konzernzentrale geflossen.
Das Unternehmen wurde erneut zum Verkauf angeboten. Ein Entsorgungsunternehmen aus Essen bekam den Zuschlag. Weil es noch mehrere Gussunternehmen erwarb, gründeten die Inhaber die Deutsche Gießerei- und Industrieholding AG (DIHAG) als Konzern. Zu den Aktionären gehörten später auch zwei ukrainische Unternehmer. 2018 geriet die Gießereibranche aufgrund von Überkapazitäten in die Krise, auch die DIHAG blieb davon nicht verschont. Wie in vielen Konzernen üblich, versuchte man, sich von Unternehmen und Beteiligungen zu trennen. „Man suchte einen Schuldigen für die Krise. Das war die Mecklenburger Metallguss“, erinnert sich Greitsch. Einzig der Ukrainer Artur Abdinov, einer der Aktionäre an der DIHAG, glaubte an die Zukunft des Unternehmens und wurde 75%iger Mehrheitsgesellschafter. Greitsch wurde mit zwei anderen Kollegen in die Geschäftsführung und zum Mitgesellschafter berufen.
Wieder einmal konnten die Warener Schiffsschraubenhersteller einem hohen Wellengang trotzen. Auch dank ihrer Technologie – die Wertschöpfungskette reicht vom groben Guss bis zur montagefähigen Schiffsschraube. Zudem ist die hohe Fertigungstiefe gut für die Eigenkapitalquote. Greitsch: „Das hat uns geholfen, die Krisen in der Schifffahrtsbranche zu überstehen.“ Der Geschäftsführer hat selbst dazu beigetragen. Der gebürtige Dortmunder, der an der Universität Rostock Maschinenbau studierte und 2009 ins Warener Unternehmen kam, hat das Retro-Fit-Programm entwickelt und eingeführt. Sein Konzept: neue Schiffsschrauben im Austausch anzubieten. „Die Reedereien stehen weltweit unter Druck, die Energiekosten und den CO2– Austausch zu senken.
Deshalb fahren Schiffe heute langsamer als früher und wir passen die neuen Schrauben exakt an die Motorisierung der Schiffe an.“ 80 dieser energiesparenden Schiffspropeller hat die Hamburger Reederei Hapag-Lloyd gerade geordert – das ist fast eine ganze Jahresproduktion. 95% der gesamten Produktion geht ins Ausland, fast ausschließlich an asiatische Werften.
Und so begegnen die Mecklenburger dem zuweilen heftigen Wellengang mit der ihnen nachgesagten stoischen Gelassenheit. Den viel zitierten Fachkräftemangel allerdings spürt das Unternehmen hingegen nicht. „An unseren speziellen Maschinen müssen wir unsere Mitarbeiter ohnehin über Monate selbst qualifizieren“, so Greitsch; er zeigt auf einen Bagger, an dessen Ende ein Bandschleifgerät zu bedienen ist. „Ein gelernter Lackierer hat den Blick auf die Fläche. Ob es eine Autokarosserie oder eine Schiffsschraube ist, es muss am Ende glänzen.“ Derweil funkeln in der letzten Werkhalle die versandfertigen Schiffsschrauben in einer mattgoldenen Farbe, mit einer Maserung, die an Fischschuppen erinnert.
KURZPROFIL Mecklenburger Metallguss GmbH
Firmensitz: Waren (Müritz)
Branche: Maritime Wirtschaft
Beschäftigte: 206
Umsatz 2023: circa 100 Mio. EUR
www.mecklenburger-metallguss.com
„Das Management vor Ort sollte aktiv einbezogen werden“
Interview mit Dr.-Ing. Lars Greitsch, Geschäftsführer, Mecklenburger Metallguss GmbH
Unternehmeredition: Herr Greitsch, Sie haben im Zuge der Herauslösung der Mecklenburger Metallguss gemeinsam mit Katrin Beuster und dem früheren Geschäftsführer Manfred Urban Anteile am Unternehmen übernommen. Was war die Motivation dafür?
Lars Greitsch: Zunächst waren wir überzeugt, dass die Expertise in der Mecklenburger Metallguss besonders im Bereich der Effizienzsteigerung von Propellern große Nachfrage erfahren wird. Die Branche stand hier unserer Ansicht nach kurz vor einem Sprung. Der kam, wenn auch verzögert, durch die weltweite Coronapandemie. Darüber hinaus war es der Wunsch unseres ukrainischen Mehrheitsgesellschafters Artur Abdinov, dass das Management vor Ort aktiv einbezogen wird.
Wie haben Sie den Kaufpreis der Anteile finanziert?
Darüber möchten wir keine Auskunft geben, weil über die gesamte Transaktion seinerzeit Stillschweigen vereinbart wurde. Viel wichtiger war zu diesem Zeitpunkt, dass unsere Hausbank, die HypoVereinsbank, eng an unserer Seite stand und uns in der Marktkrise weiterhin finanziert hat. Eine enge Abstimmung und ein lückenloses Berichtswesen waren hier die vertrauensbildenden Maßnahmen.
Wird diese Übernahme der Gesellschaftsanteile nur vorübergehend sein?
In diese Richtung ist nichts geplant. Ich möchte noch einige Jahre arbeiten und mich auch als Gesellschafter aktiv weiter einbringen, weil wir hervorragende Perspektiven für den Schiffspropellerbau an diesem Standort sehen.
Herr Greitsch, wir danken Ihnen für das interessante Gespräch!
Dieser Beitrag ist in der Unternehmeredition-Magazinausgabe 4/2023 mit Schwerpunkt “Unternehmervermögen” erschienen. Zum E-Paper geht es hier.